Ndfeb hydrogen decrepitation.jpeg
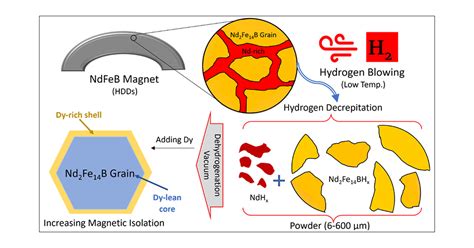
Mar 1, 1985 · The hydrogen decrepitation (HD) process are studied in detail based on these results. The hydrogen absorption mechanism of Sm(CoFeCuZr) 7.6 alloy can be regarded as a hydrogen dissolution process without phase transformation. In addition, the existence of a large amount of fine grains in the SC has an adverse effect on the alignment, which can ... Jul 8, 2020 · The application of hydrogen decrepitation (HD) as a process for recycling Nd-Fe-B sintered magnets was reported in [ 6 ], in which the essential role of hydrogen in the recycling process was demonstrated. The obtained magnetic properties of the recycled magnet were ( BH) max = 290 kJ/m 3 (±5 kJ/m 3 ), Br = 1240 mT (±50 mT) and jHc = 830 kA/m ...
Did you know?
Hydrogen absorption and desorption characteristics for high coercivity NdDyFeCoNbCuB sintered bulk magnets were studied, by differential scanning calorimetry (DSC) measurement and hydrogenation kinetics measurement. The DSC measurements showed that hydrogenation of Nd-rich phase occurred in the temperature range of …Jul 8, 2020 · The application of hydrogen decrepitation (HD) as a process for recycling Nd-Fe-B sintered magnets was reported in [ 6 ], in which the essential role of hydrogen in the recycling process was demonstrated. The obtained magnetic properties of the recycled magnet were ( BH) max = 290 kJ/m 3 (±5 kJ/m 3 ), Br = 1240 mT (±50 mT) and jHc = 830 kA/m ... The extracted NdFeB powder is of a purity whereby it can be re-processed into new magnetic materials or rare earth alloys. HyProMag Ltd will be targeting a wide range of end of life applications. Illustration of the HPMS process applied to the voice coil assembly of a hard disk drive. Pilot HPMS reactor capable of processing 5kg of NdFeB.calcium [12] and hydrogen decrepitation [1,13-19]. Many of these are under current development. Hydrogen decrepitation (HD) is based on the selective synthesis of neodymium hydrides though the reaction of hydrogen gas with neodymium located in the Nd-Fe-B magnet. HD process was originally designed and patented by Harris et al. (1979) as a way to The processing and characterisation of recycled NdFeB-type sintered magnets. M. Degri. Materials Science, Engineering. 2014. A study of the processing and characterisation of sintered NdFeB magnets made from recycled feed stock was undertaken. Initially the hydrogen decrepitated (HD) powder was investigated using two…. Expand. Fig. 1. Illustration of the Hydrogen Decrepitation Press-Less Process (HD-PLP) recycling of anisotropic sintered NdFeB magnet. Passivated commercial N48M sintered magnets were used as starting material and hydrogen was applied to disintegrate the magnets inside a ball milling container. The hydride powder was both used directly …Hydrogen Decrepitation is a process step used in the production of Neodymium magnets to create extremely small grains in the material. Neodymium magnets must have very small grains averaging about 5 micrometers in order to have the best magnetic properties. But the grain sizes after casting are much larger than that, so they must be ground down ...International Journal of Hydrogen Energy Volume 22, Issues 2–3 , February–March 1997 , Pages 241-244 Technical and operating features of interaction between hydrogens and alloys and magnets on the basis of rare earth metalsThis means that NdFeB magnets are prone to galvanic corrosion, in particular, intergranular corrosion attack. The corrosion mechanism as well as the hydrogen decrepitation behaviour of microcrystalline (i.e. sintered) magnets has been studied extensively [11], [12], [13], [14].A high performance sintered NdFeB magnet with N52 was prepared by strip casting, hydrogen decrepitation, jet milling, rubber isostatic pressing with impulse magnetic field and vibrating. The structure of the magnet was investigated by XRD, optical microscope, TEM and SEM, and its demagnetization curve was tested by magnetograph. The results …There are many major production steps –plus numerous sub steps- in the manufacture of high-quality, high-tech Neodymium magnets. Each step is highly important, and each step is an essential part of a highly refined …The MMG has been active in the field of rare earth alloys and processing of permanent magnets using hydrogen for over 40 years. Originated by Professor Emeritus Rex Harris, the hydrogen decrepitation method, which is used to reduce NdFeB alloys to a powder, is now ubiquitously employed in worldwide magnet processing. Semantic Scholar extracted view of "Possible methods of recycling NdFeB-type sintered magnets using the HD/degassing process" by M. Zakotnik et al. ... The purpose of this thesis was to study the Hydrogen Decrepitation (HD) process as a way to recycle waste scraps of Nd-Fe-B sintered magnets into highly coercitive and anisotropic …Hydrogen Decrepitation and Recycling of NdFeB-type Sintered Magnets. Miha Zakotnik, E. Devlin, +1 author. A. Williams. Published 2006. Materials Science, Engineering. Journal of Iron and Steel Research International. View via Publisher. Save to Library.Hydrogen decrepitation (HD) of Nd-Fe-B cast alloys is widely used in the processing of sintered magnets. The oxidation resistance under air of alloy powder …The hydrogen treatment of the Nd‐Fe‐B alloy ingots was found to produce magnet powders with good magnetic properties. Typical magnetic properties of these powders are as follows; 4πIs = 9.5 kG, Br = 7.7 kG, iHc = 9.4 kOe, and (BH)max = 12.2 MGOe. Microstructural studies of these powders showed that they are made of fine …High performance NdFeB permanent magnets are widely manufactured using the conventional powder metallurgy route involving distinct steps: alloy synthesis by strip casting, pulverization by hydrogen decrepitation and jet milling, shaping by compaction and sintering followed by annealing [32]. Every step of this manufacturing process has …The hydrogen-absorbing NdFeB powder absorbs heat in the plasma and rapidly decomposes and dehydrogenates. At the same time, in the dehydrogenation process, the particles are cracked and broken to form fine NdFeB powder due to rapid heat absorption and release of a large amount of hydrogen, and the NdFeB powder is at a high …The nature of hydrogen decrepitation when applied to a cast Nd-Fe-B permanent magnet alloy has been studied by following the microstructural changes on polished surfaces of the material exposed to hydrogen at a pressure of 4 bar. The milling of the material decrepitated at a pressure of 10 bar has also been studied by determining …The Hydrogen Decrepitation and the Hydrogen Disproportionation Desorption Recombination processes for the preparation and the recycling of the two industrially produced phases of SmCo alloys, SmCo5 and Sm2Co17, are reviewed. The effects of the chemical composition, the microstructure, the exposure time, the hydrogen …Michihide Nakamura, Masashi Matsuura, Nobuki Tezuka, Satoshi Sugimoto, Yasuhiro Une, Hirokazu Kubo, Masato Sagawa; Preparation of ultrafine jet-milled powders for Nd-Fe-B sintered magnets using hydrogenation–disproportionation–desorption–recombination and hydrogen …May 11, 2020 · Metallurgical simulation and evaluation of the resource efficiency of whole production processes are of key importance for sound environmental impact assessments. Exergy dissipation analysis is suitable to quantify the theoretical limits of a process and pinpoint hotspots for improvements along the value chain. Production of NdFeB permanent magnets is evaluated herein using a simulation-based ... Jan 1, 2007 · The rapid cooling of the strip flakes suppresses the growth of soft α-Fe branch crystal grains. The thickness of the strip flakes was about 0.25–0.35 mm. Hydrogen decrepitation (HD), which uses the expansion of hydrogen to break up the flakes, was followed by milling in a jet mill (JM). The particles were then accelerated to supersonic ... Hydrogen decrepitation (HD) of the sintered block was used to return the annealed material back into a powder [33]. During this step, the material reacts with hydrogen resulting in volume expansion of both the Nd-rich phase, at triple junctions and grain boundaries, and the Nd 2 Fe 14 B matrix phase [34]. This expansion leads to …
Hydrogen decrepitation (HD) of Nd-Fe-B cast alloys is widely used in the processing of sintered magnets. The oxidation resistance under air of alloy powder …The reaction speed in the typical hydrogenation run (Fig. 1b, 1d) is limited only by the rate of the gas diffusion into the sample.When the reaction proceeds in deficiency of hydrogen (Fig. 1b) only a part of the Nd transforms into neodymium hydride NdH y as it follows from the diffraction pattern displayed in Fig. 2d.That pattern includes …Each magnet was exposed to hydrogen and the decrepitation behaviour observed. The anisotropic samples were found to decrepitate exclusively from the ends of the rods whereas the isotropic magnets were attacked by the hydrogen at all points on their surface. Bulk corrosion studies in steam gave comparable results, the oriented sample …Nov 15, 1988 · A combination of hydrogen decrepitation (HD) and jet milling (JM) has been used to produce powder for the processing of permanent magnets. The procedure has proved to be very successful for both NdFeB (Neomax) alloys and the NdDyFeNbB high coercivity alloys.
Sep 20, 2016 · Hydrogen decrepitation of Pre-dismantled Computer HDDs. The University of Birmingham (UK) has developed a hydrogen-processing method to extract sintered NdFeB magnets from computer hard disk drives [13, 41]. During this process, either the voice coil assemblies from the hard disk drive or the cropped corner from the drive is exposed to hydrogen ... An essential information about history and applications of Hydrogen Decrepitation has been generally reported. Very important technical details about the HD route were summarized, as well as fabrication procedure of Nd16Fe76B8 permanent magnet. Some micro strucural of SEM images of hydride and sintered magnets were given to ……
Reader Q&A - also see RECOMMENDED ARTICLES & FAQs. The processing and characterisation of recycled NdFeB based magne. Possible cause: During the hydrogenation process, a volume expansion takes place, which promotes the fo.
A study of the processing and characterisation of sintered NdFeB magnets made from recycled feed stock was undertaken. Initially the hydrogen decrepitated (HD) powder was investigated using two different milling techniques ball milling and burr milling. The powders were analysed with optical microscopy, with the aid of a magnetic field.International Journal of Hydrogen Energy Volume 22, Issues 2–3 , February–March 1997 , Pages 241-244 Technical and operating features of interaction between hydrogens and alloys and magnets on the basis of rare earth metalsNov 15, 2021 · After the hydrogen decrepitation process, the powders were pulverized by either He-jet milling or N 2-jet milling, obtaining a powder with a particle size of ~0.8 µm for the HDDR processed and He-jet milled sample, ~1.0 µm for the He-jet milled sample, and ~3.0 µm for the N 2-jet milled sample.
The rapid cooling of the strip flakes suppresses the growth of soft α-Fe branch crystal grains. The thickness of the strip flakes was about 0.25–0.35 mm. Hydrogen decrepitation (HD), which uses the expansion of hydrogen to break up the flakes, was followed by milling in a jet mill (JM). The particles were then accelerated to supersonic ...The influence of the alloy granulation grade, temperature and surface oxidation on the kinetics and the course of the fracture processes during the hydrogenation of Nd16−xDyxFe76B8 (x=0–3) alloy was studied. The average particle sizes of the alloy were 1 mm, 5 mm and 3 cm and the temperature range between 20 and 200 °C. Pre-oxidation …
Jan 1, 2022 · The SC alloy is converted into Hydrogen decrepitation and recycling of NdFeB-type sintered magnets. M Zakotnik, E Devlin, IR Harris, AJ Williams. Journal of iron and steel research, international 13, 289-295, 2006. 57: 2006: Life cycle assessment of emerging technologies on value recovery from hard disk drives.Jul 15, 2015 · The obtained strips were pulverized and further milled into ∼5 μm powder using hydrogen decrepitation and jet milling, respectively. These powders were pressed in a magnetic field of 1.8 T under a pressure of 8.0 MPa. Afterward, the green compacts were sintered at 1070°C for 3 h in vacuum, cooled by Ar quenching. Jan 1, 1991 · The subject of this paper is methThe subject of this paper is method (4) together with other aspects Mar 1, 2019 · The Hydrogen Decrepitation process (HD) is used as an alternative method of powder preparation in the manufacturing process of sintered Nd Fe B magnets [ 1]. During the HD process a NdFeB-type material is hydrogenated by gaseous hydrogen at atmospheric (or elevated) pressure at room (or elevated) temperature. The influence of the alloy granulation grade, temperature and surface oxidation on the kinetics and the course of the fracture processes during the hydrogenation of Nd16−xDyxFe76B8 (x=0–3) alloy was studied. The average particle sizes of the alloy were 1 mm, 5 mm and 3 cm and the temperature range between 20 and 200 °C. Pre-oxidation … The hydrogen treatment of the Nd‐Fe‐B alloy i magnets. The thermal and mechanical impact of the hydrogen decrepitation process was assessed during hydrogen processing. For all forms of sintered NdFeB scrap the surface condition of the magnets is important as oxidation has been shown to inhibit the onset of the hydrogen decrepitation process. In this Hydrogen decrepitation and recycling of NdFeB-type sinteredThe powders were produced by hydrogen decrepitation and onThe room temperature hydrogenation causes decre Due to the high strength and very compact structure of sintered NdFeB magnets, hydrogen decrepitation is a necessary step to break down the magnet mass. On the other hand, the resin-bonded NdFeB magnets have very low strength and can be easily crushed by heating and removing the resin and epoxy used in their fabrication. 39. 3.The gravimetric measurements also confirmed that Dy additions increase both the initiation and absorption time for hydrogen decrepitation. Hence, a higher hydrogen pressure will be required to speed up the process. AB - Scrap containing NdFeB is a valuable resource for the production of NdFeB magnets as the demand for these materials grows. Broadening the knowledge about the hydrogen decrepitation of NdFeB permanent magnets have different life cycles, depending on the applications: from as short as 2–3 years in consumer electronics to 20–30 years in wind turbines. The hydrogen treatment of the Nd‐Fe‐B alloy ingots was found to pro[The Hydrogen Decrepitation and the Hydrogen DisproThe intrinsic magnetic coercivity (Hci) of Nd‐Fe‐B‐based per A combination of hydrogen decrepitation (HD) and jet milling (JM) has been used to produce powder for the processing of permanent magnets. The procedure has proved to be very successful for both Nd-Fe-B (Neomax) alloys and the ND-Dy-Fe-Nb-B high coercivity alloys. The magnets produced by the HD/JM process showed excellent coercivities when …